What do “gecko feet“ and intelligent robotic gripping systems have in common?
Saarbrücken, December 9, 2022
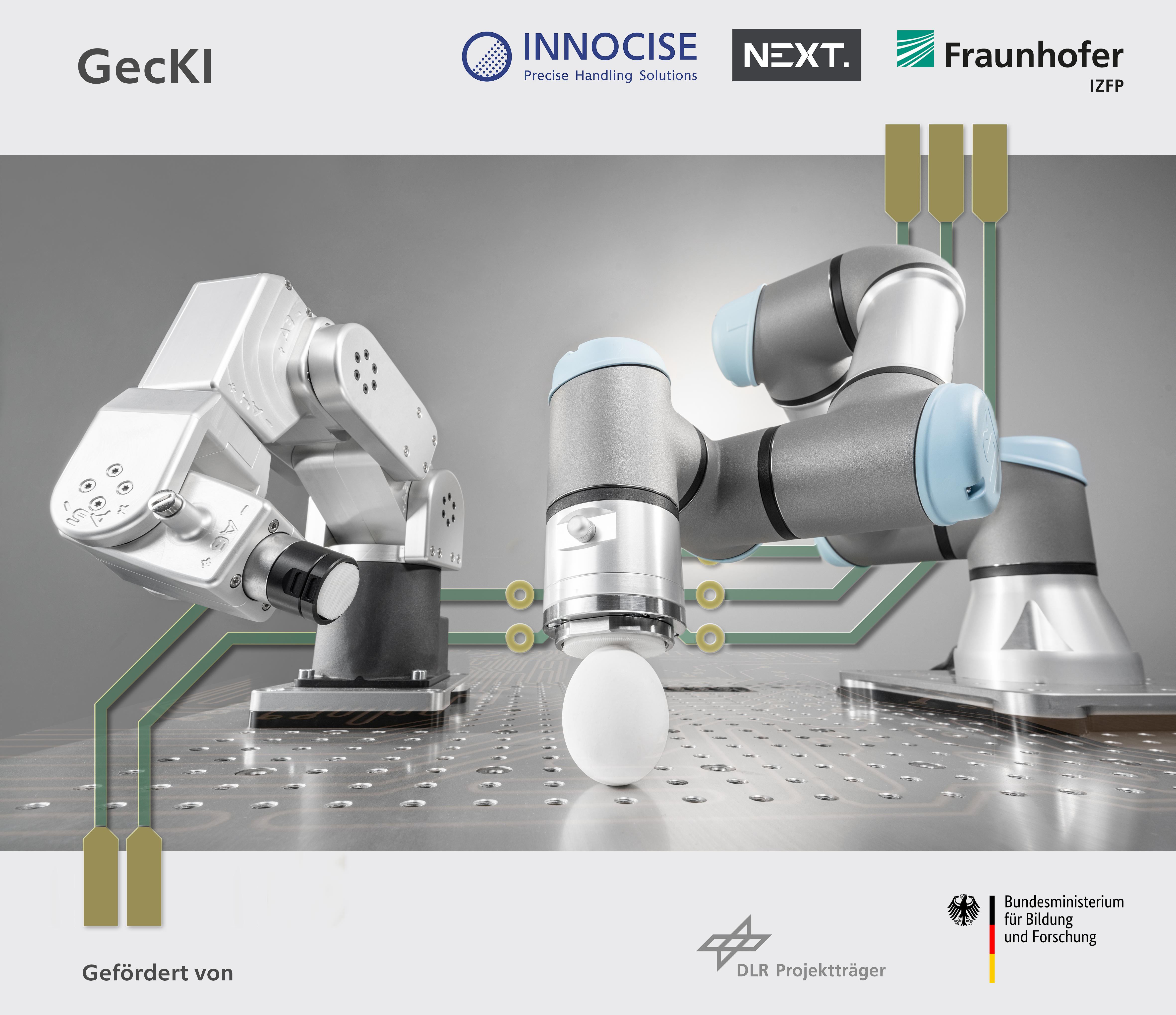
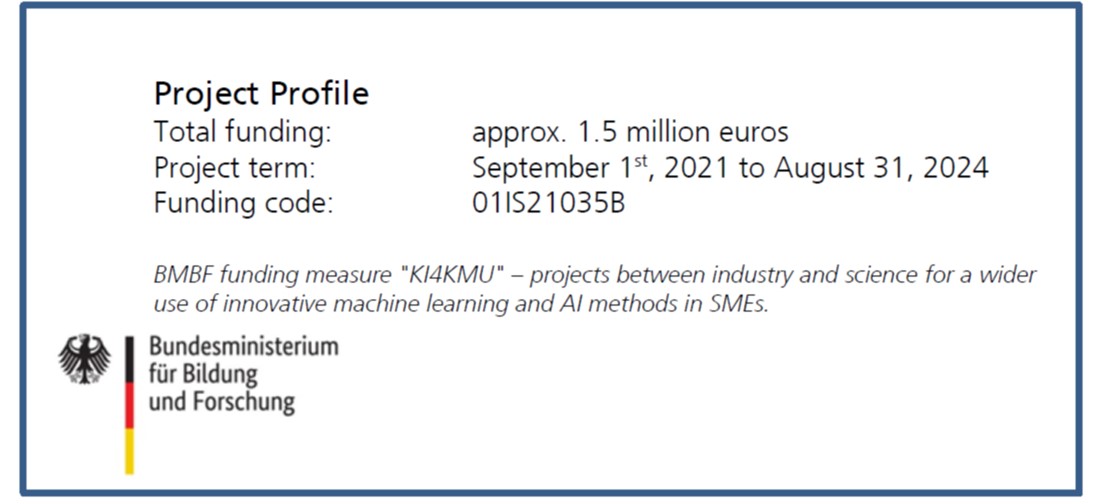
No wall is too steep for them, they walk upside down on ceilings, their fine-haired feet stick better than any professional glue without leaving any traces, and they defy gravity: the feet of geckos! They are of equal interest to researchers in materials science and in AI research. This effect of the gecko's feet is now to be exploited in the joint project “GecKI“ to develop energy-efficient, auto-adaptive and product-independent adhesive pads for robotic gripping systems. The German Federal Ministry of Education and Research (BMBF) is funding “GecKI“ with approx. 1.5 million euros.
How can artificial intelligence be used to create a robot gripping system that is as versatile and energy-efficient as possible? Moreover, how can this system trigger a leap in development in the use of intelligent, self-regulating and flexibly scalable handling processes for SMEs and large companies likewise? This research and development task is being addressed by the Fraunhofer IZFP, a research and development institute located at Saarland University, INNOCISE GmbH, a spin-off from INM – Leibniz Institute for New Materials – and NEXT. robotics GmbH & Co. KG.
The objective of the project is to refine artificial intelligence methods to design a novel sensor system which enables the auto-adaptive, robotic manipulation of objects using its own object recognition: the robot arm is provided with the ability to sense the type of the product and to adapt itself accordingly.
Intelligent and adhesive gripping systems inspired by a natural model
In highly flexible and frequently changing production lines as well as in demanding environments such as clean rooms or in a vacuum, cost-effective and resource-saving robot-assisted gripping systems are needed. To this end, adhesive grip pads attached to the robot arm are to be equipped with intelligent sensors and then be used in production lines independently of the product. The range of applications is huge and spans from sensitive objects or surfaces to heavy loads e.g., fiber glass or car doors as two examples of countless. The role models for this are provided by the feet of geckos, which, among other desirable properties, have the ability to hold substantial loads. In doing so, they make use of the physical adhesion based on the intermolecularly acting Van der Waals forces – they walk and climb without leaving any traces.
The research project will render the innovative adhesive pads from INNOCISE intelligent. “In addition, the robot control intelligence will translate the information and data obtained from this sensor intelligence into auto-adaptive motion sequences,“ explains Simon Herter, a scientist at Fraunhofer IZFP. Another advantage in this era of drastic energy savings is that the pads do not require an external energy supply such as a vacuum or a magnetic gripper. This greatly expands the range of applications on modular production lines. The integration of the pads into industrial lines could follow the “plug-and-play“ principle. Their widespread use can greatly improve the energy efficiency of manufacturing-related handling processes.
First milestone to sensing
A first important milestone was achieved with the design of a test rig. “With the help of this demonstrator, we are able to visualize robotic gripping contact and its structures. We have developed first sensor prototypes that can enable bioinspired grippers to feel,“ explains Dr. Sarah Fischer, the responsible principle investigator at Fraunhofer IZFP.
The “GecKI“ research project is intended to contribute to a substantial increase in the economic efficiency of flexible and changing productions. Because of this increase, Germany will remain competitive as a business location and take a leading role in the field of technological innovations for highly flexible production techniques. As part of the “KI4KMU“ measure, the BMBF is funding the joint project “AI-based object recognition and adaptive control for intelligent, bio-inspired robot gripping systems for embedding in Industry 4.0 environments (GecKI)“ with approximately 1.5 million euros.
More on Fraunhofer IZFP:
Fraunhofer IZFP is an internationally networked research and development institute in the field of applied, industry-related research located in Saarbrücken. The activities of the Institute, founded in 1972, zero in on the development of complex, cognitive sensor and data systems for safety, sustainability and efficiency. These systems are tailor-made for the optimization of individual cycle phases or the overall cycle. They are then transferred to application with technology companies. Furthermore, the understanding of technical testing and sensor physics is complemented by technologies and concepts from AI research. Fraunhofer IZFP currently employs about 120 people as permanent staff.