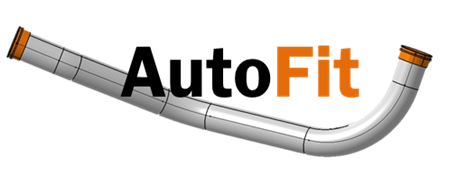
The aim of the joint LuFo project “AutoFit“ was to increase the efficiency and competitiveness of the production of high-tech pipelines in the aviation sector through automation and digitalization. This is necessary in order to meet the increasing social, political and economic requirements for increasing the efficiency of production processes and the growing competitive pressure.
To this end, an automated assembly cell was successfully set up and tested in laboratory operation during the course of the project. The positive results show great potential, particularly through increased cost-effectiveness, efficiency and quality. The digital documentation of the process parameters improves traceability and quality assurance.
As part of the development of the automated placement cell, various non-destructive testing methods were investigated and further developed with regard to their suitability for inline determination of the connection quality produced. In the future, this can ensure continuous safeguarding of the production process and testing of the connection quality and all manufactured pipe-fitting connections, thereby reducing throughput times as well as material and personnel costs in series production (resource conservation and efficiency). Furthermore, the avoidable or reduced use of etching agents in the conventional metallographic examination can reduce health risks, increase occupational safety and contribute to environmental protection.
In the course of the project, new types of measuring equipment were also tested to determine the internal diameter of joined pipe-fitting connections, which reduce testing time and increase measuring accuracy.
In addition, an “intelligent“ plastic injection-moulded fitting was developed and tested, which has great potential for aircraft with fiber composite wings due to its electrical properties. Various assembly processes were tested. The results show that the developed fitting has both the required electrical conductivity and fluid tightness.
The project consortium consisted of PFW Aerospace GmbH and Steitz Präzisionstechnik GmbH on the business side and the Institute of Forming Technology and Lightweight Construction (IUL) at TU Dortmund University and Fraunhofer IZFP on the research side.
The project was funded by the Federal Ministry of Economic Affairs and Climate Action (BMWK) as part of the “National Civil Aviation Research Program LuFo VI-1, Program Line (C) Technology“ (funding reference: 20W1905D). The project partners would like to thank the German Aerospace Center (DLR), the Project Management Agency for Aeronautics Research on behalf of the BMWK for the financial support and organizational supervision of the project.