Intelligent self-optimizing plants: 3MA for monitoring and controlling sheet metal forming
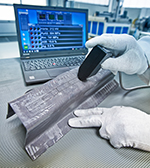

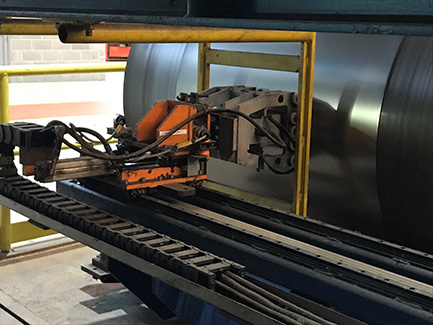
In sheet metal forming, increasingly high demands are being placed on components and processes. Even in deep drawing below the recrystallization temperature, increasing process complexity, ever smaller sheet thicknesses, and batch fluctuations are making it increasingly difficult to ensure consistently high process reliability. Sporadic tearing, necking, and wrinkling are the result. The 3MA sensor allows steel sheet properties to be characterized in the pre-process, avoiding scrap. Stricter safety requirements and the demand for reduced fuel consumption or increased range in vehicles with internal combustion engines or electric motors are steadily increasing use of hot-formed (press-hardened) components in automotive engineering. For these safety-relevant components’ production quality (crash resistance) to be assessed, they must be randomly tested for hardness, strength, etc. This is where the 3MA sensor is used in the post-process to reduce time-consuming, costly destructive testing.
3MA exploits the fact that the same microstructural features of the steel influence both its mechanical/technological and its nondestructively measurable magnetic properties. These correlations are used to nondestructively determine forming and strength properties. Subsequent forming processes can be controlled on the basis of the forming properties measured in a steel strip or in blanks already cut to size. On the other hand, the strength properties of components already formed can also be tested. 3MA is now an established quality inspection method for PHS (press-hardened steel) components.
Fields of application
The 3MA sensor is placed on the component manually or by a robot. Within a few seconds, the determined values (hardness, tensile strength, yield strength, elongation at break and uniformity elongation, N-value and R-value, and the properties of the coating if there is one) are displayed. Non-contact measurements are also possible. For continuous in-line strip steel testing, a customized 3MA sensor is installed about 5 to 6 mm above or below the strip. Alternatively, this sensor can be used during the pass to inspect blanks that have already been cut to size in. Various interfaces, including OPC UA, are available in the software for the data connection to production.