Smart sensors for efficient processes
Press Release / October 16, 2017
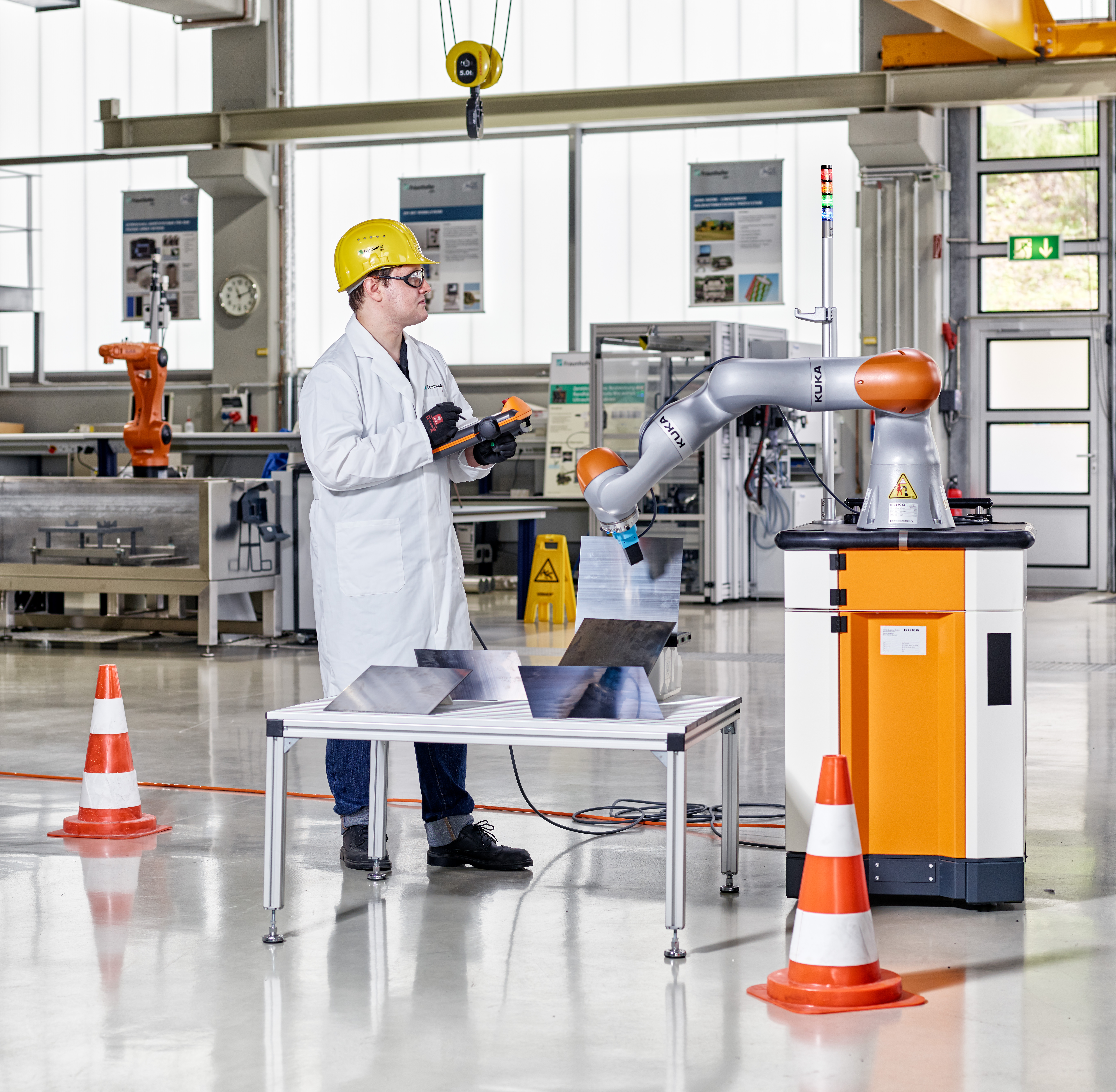
Material defects in end products can quickly result in failures in many areas of industry, and have a massive impact on the safe use of their products. This is why, in the field of quality assurance, intelligent, nondestructive sensor systems play a key role. They allow testing components and parts in a rapid and cost-efficient manner without destroying the actual product or changing its surface. Experts from the Fraunhofer IZFP in Saarbrücken will be presenting two exhibits at the Blechexpo in Stuttgart from 7–10 November 2017 that allow fast, reliable, and automated characterization of materials and detection of defects (Hall 5, Booth 5306).
When quality testing uses time-consuming destructive test methods, it can result in enormous costs due to damaging or destroying the products. And given that testing is restricted to random sampling, faults in processes are often not found until a large amount of scrap has already been produced. Consequently, nondestructive testing method represent an alternative, and after appropriate adaptation processes, also a replacement for destructive methods for the long run.
Cognitive sensors for quality assurance in production
At this year's Blechexpo, our engineers will demonstrate a robotics-supported sensor system that can rapidly and easily be integrated into production processes. The automated application of intelligent, nondestructive sensor systems is not only essential for ensuring optimum product quality in production, it is also indispensable for realizing current machine learning concepts. The potential use of such systems will be demonstrated in an exemplary case of robotics-supported testing of press-hardened parts by means of EMAT* and 3MA**. EMAT allows couplant-free testing of defects in sheet metal, while parallel application of 3MA makes quantitative material characterization possible.
Testing within seconds
The advantages of the robotics-based combination of the two sensors (3MA, EMAT) include rapid testing in mere seconds, determining and evaluating several relevant quality characteristics, as well as the nondestructive testing of sheet metal. "The combined sensor-based testing process allows early detection of mechanical properties, e.g., the residual stress and the hardness of steel, as well as defects like cracks or necking. This will save resources, reduce costs, and contribute to strengthening manufacturers' competitive position," explained Frank Leinenbach, development engineer at the Fraunhofer IZFP. The institute has decades of experience and expertise in combining and automating nondestructive testing methods for production.
* EMAT: Electromagnetic acoustic transducer
** 3MA: Micromagnetic multiparameter, microstructure, and stress analysis
Quality assurance during steel production
The steel-producing and -processing industries need nondestructive testing methods in quality assurance. Frequently relevant quality characteristics include hardness, case depth, strength, and residual stresses. In this context, nondestructive micromagnetic testing methods are optimally suited for providing fast and reliable statements on the quality status of ferromagnetic materials. "An inspection task that is being requested frequently is the monitoring of heavy steel plates, and the related detection of localized increases in surface hardening," explained Sargon Youssef, researcher and engineer at the Fraunhofer IZFP. These localized effects can be detected by means of micromagnetic measuring effects when the 3MA-X8 testing technology developed at the Fraunhofer IZFP is applied. The specific strengths of the 3MA-X8 testing system lie in its user-friendly learning curve and calibration, as well as in its variable and robust sensor design. A key point is the test system's multi-channel real-time capability.
The 3MA-X8 testing method will be demonstrated at the Blechexpo in Stuttgart using a fair exhibit. As under realistic conditions, our high-tech testing technology will be integrated in a miniaturized rolling line. Here, sheet metal to be tested will be measured using the testing method, detected, and sorted – if necessary – into "OK sheet metal" or "not-OK sheet metal".
Schematic layout of a rolling line for nondestructive testing of heavy plates
©Fraunhofer IZFP