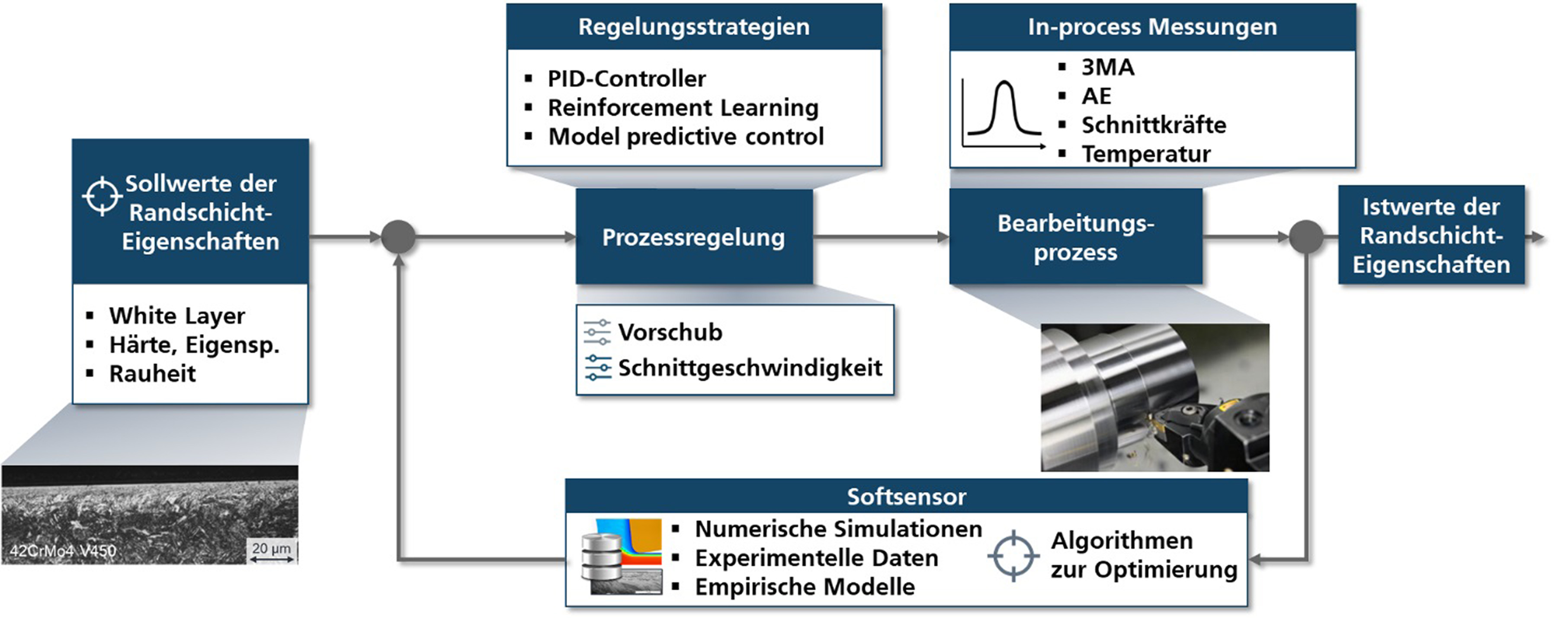
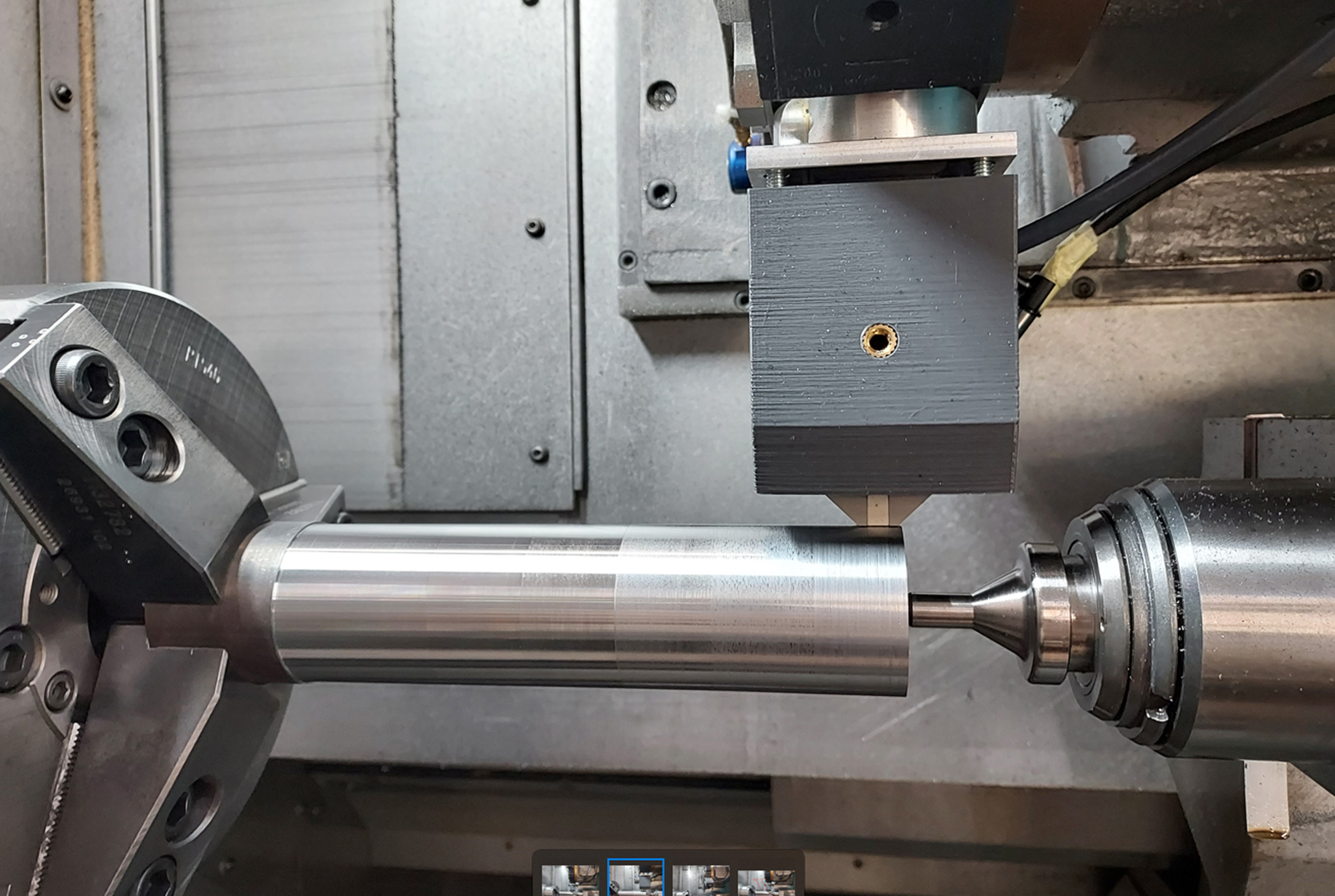
When machining steels, variations in the process parameters can lead to significant changes in the thermal and mechanical load on the workpiece. These loads can cause a modification of the near-surface microstructure, which appears as a white layer in the micrograph. They can contain cracks and residual tensile stresses, which have a negative effect on the service life of the workpiece and must be avoided.
The aim of the “Process-integrated soft sensor technology for surface conditioning during external longitudinal turning of 42CrMo4” research project is to develop an in-process-capable, multisensory and modularly expandable control concept in order to set a defined surface layer condition that may be composed of several target variables. This control concept is implemented as an example for the application of external longitudinal turning of 42CrMo4.
The 3MA testing technique is suitable for the sensory detection of differences in the surface layer of components, even at machining depths of less than 10 µm and thus for detecting the beginning of the formation of the white layer. In addition to the 3MA micromagnetic method, the acoustic emission method is also to be used in NDE multisensor technology in order to derive information about the formation of white layer and undesirable residual stress changes as well as indications of tool wear.
Procedure:
- Experimental analysis of external longitudinal turning
- Simulation of external longitudinal turning
- Development and process integration of NDE multi-sensor technology
- Soft sensor synthesis
- Integration and calibration of the soft sensor
- Determination of measurement uncertainty
- Realization and further development of the multimodal soft sensor
- Inline measurements using 3MA and acoustic emission
- Process strategy optimization and model extension
- Implementation of control concepts and validation